CONTACT US
Mobile Phone : 008618625531588
Fax : 0086-0371-86151367
E-mail : hlmachine001@gmail.com
E-mail : fancy001@hycfm.cn
Address : No. 285, Floor 18, Unit 1, Timing Senlin International Building, Cross Of Tianming Rd. And Dongfeng Rd., Jinshui Dist., Zhengzhou, Henan, China (Mainland)

Nuts Processing Machine
Pneumatic peeling machine
- Capcity: 250--300kg/h
- Power: 15-22KW
- Voltage: 380V/50HZ
- Ports: Qing Dao
- Size: 960×710×1660mm
- Payment: T/T Western Union L/C

(※ Click this button to inquiry)
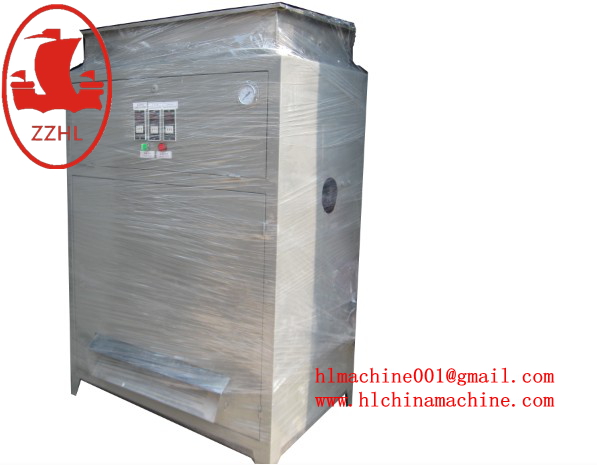
Pneumatic peeling machine manual
Functions and features
ST-150 is the machines that can automatically remove the peels of separated cashew, peanuts, soybean and pine nuts with a dry-type pneumatic processing technology, which can produce smooth and non-damage nuts reaching the national environment-protection and sanitation standards, as well as requirements for export.
The machine is driven by an air compress and uses pneumatic power to remove the out skin of the nuts with different sizes. It is applied to agricultural products with membrane. The machine is widely used for deep processing of garlic, by food processing factories, mines, army’s and schools’ dining rooms, vegetable distribution centers, agricultural produce fairs and other processing units and individuals.
Installation and trial run
After removing the packing materials of the peeler, mount it on the level ground in the room. Connect the ground wire, connect it to the power supply that meets the requirements of voltage and frequency as per the product instruction, and then connect the machine to the air compressor whose specifications including power, pressure and air flow rate match the peeler.
The air compressor is an air-pressure started machine. The air pressure and airflow rate it generates must meet the requirements of the garlic peeler. Specifically, the air flow rates for the above 3 models are respectively 1.06m3/min, 1.6m3/min, and 3.2 m3/min. The power values of the motors of these air compressors are: 7.5KW for ST-150, 11KW for ST—300 and 22KW for ST—600. The power supply of them is 380V /50HZ. Only when all these requirements are met, can the peelers work nonstop. When installing a peeler, the installers should connect the air-in pipe or its connection joint under the peeler to the outlet of the air compressor’s air-discharging valve. A quick connector is not allowed to be used here in case the airflow rate would be affected. The total length of the high-pressure connecting pipe connecting the air compressor and the peeler shall not be longer than 15m. The air pipe’s diameter shall be the same as the peeler’s air inlet pipe so as to avoid loss of air pressure and flow rate into the peeler.
Connection to the power supply: The peeler has already been equipped with connecting wires to external power supply; the user should use the connecting wires with the same specifications as them. The electric brake shall be equipped with connecting wires to external power source; the user shall use the connecting wires with the same specifications as them. The electric brake’s current capacity shall be over 30A.
Adjustment of the electric panel should be conducted without voltage on:
1 ,Time relay: The electric panel is equipped with 3 time relays, respectively controlling the time lengths of feed-in, peeling, and discharging. The adjustment of them is directly related to the quality of the peeler’s work, namely, the peeling performance and wounding degree; so it’s necessary to adjust them carefully.
The normal controlled scope: Feed-in time 1~2 second Peeling time 4~10 seconds Discharging time 3 seconds
The length of feed-in time, or in other words, the amount of garlic clove fed into the machine, and the length of peeling time can influence the peeling performance.
When all necessary adjustments are completed, start up the air compressor; when the air pressure reaches the values mentioned above, switch on the power of the peeler, and the peeler starts to work.
Method of operation
1. Check whether the ground wire is in proper condition:
Check to see whether the power supply is 220v/50Hz, whether the load on the wire matches the peeler, and whether the rotation of the air compressor is in the right direction.
2. Adjustment for time of feed-in, peeling, and discharging:
This is critical because it directly influences the quality and efficiency of the peeling.
Normal adjustment scope: feed-in time: 1-~2 second, peeling time 4~10 seconds, discharging time: 3 seconds(for example : the pressure of cashew is 4-- 5kg. peeling time is 4--5.s. peeling rate: 80%. Complete rate: Min95%)
Setting of feed-in time:
The setting of it should follow a principle of adjusting from low value to high value. The peels discharged into the peeling bucket under the machines is normally about 0.4 kg for ST-150, 0.8kg for ST-300 and 1.6 kg for ST-600. If too much materials is fed into the peeler, it will affect the peeling performance, i.e., the peeling is incomplete. Too little materials fed into the peels would also affect peeling performance, or even whole materials may be discharged out from the peeler’s discharging end.
(2) Setting of peeling time:
Setting of peeling time is directly related to the air compressor’s air flow rate and air pressure, as well as to the amount of garlic fed into the peeler.
The peeling time is normally set between 4 and 20 seconds. If he garlic is relatively dry, or belongs to the species relatively easy to be peeled, the time value should be set lower. If not so, the time value should be set higher. A too low time value might make it more difficult to remove peel of the garlic or might lower the peeling performance. But a too high time value would make it highly possible for garlic surface to be wounded. So the user should adjust the peeling time according to the season, garlic species, and the places of production. Before mass production, or during production, the user should appropriately adjust the value some times according to concrete conditions. When the peeling performance is relatively satisfactory, it is advised to begin mass production.
(3) Setting of discharging time:
Discharging time is normally set at about 3 seconds. If it is too low, discharging would be incomplete, while if it is too high, it would cause waste of time and consequently low production efficiency. If the power of the air compressor is too low to satisfy the peeler’s need of airflow rate, the user can appropriately adjust the discharging time to a higher value to solve it.
Note: Setting of the four above values, namely, values for heating, feed-in, peeling, and discharging must be conducted without power on.
4. When the all 4 the values mentioned above are set, pour the materials to be peeled into the feed-in bucket. Start the air compressor, and when the pointer needle of the pressure gauge on the panel reaches the value specified in the table above, switch on the power. Then turn on the heating switch. If no heating is needed, or the peeler is not equipped with a heater, the user may directly switch on the power and the peeler will start to work.
During mass production, the user should check the oil-water separator-filter on the back of the peeler and discharge it if too much water has accumulated in it. The Storage bucket should remain higher than half of the total capacity and should be timely replenished to make up for shortage and to achieve effective drying so that the peeler’s peeling performance would not be affected due to insufficient drying , or its feed-in amount does not have to be changed due to shortage of products. (Note: materials to be peeled should be as low as possible to avoid negative influence on fed-in amount.) During operation, if the system displays some abnormal signs, the user shall cut off the power supply timely and then restart the machine, which will usually set the machine back to a normal status. When all work is finished, the user shall switch off the power.
Maintenance of the device
During the use of the peeler, it is necessary to check various parts of the device and make sure they are in good condition. Repairs should be done immediately whenever any problem is spotted.
During the production, the peeling bucket must be cleaned at a certain interval. Once the products are found less clean, the peeling bucket must be cleaned immediately.
There is a drainage switch located at the lower part of the oil/water separating filter. Frequently activate the switch to drain the moisture so as to keep the air dry. For the type with triads, oil shortage must be prevented in the oil storage bucket so as to ensure the peeling effect and protect the components.
Frequent checks shall be done to the various components and pipelines in the airflow circuit. Once a leakage is spotted, immediate repairing and replacement of components or pipelines must be done.
(II) Technical data
Model | ST-150 | ST-300 |
Capacity | 100--150kg/h | 250--300kg/h |
Air inflow rate | 1.05m³/min | 1.60m³/min |
Air inflow power | 7.5KW/380V/50HZ | 15-22KW/380V/50HZ |
Air compressor | 0.4-0.6Mpa | 0.8-0.9Mpa |
Non-heating single machine power | 0.2KW/220V/50HZ | 0.2KW/220V/50HZ |
Peeling rate | 95-98%
|
95-98%
|
Oversize | 640×600×1300 | 960×710×1660 |
Weight | 70kg | 110kg |
Phenomenon | Cause of faults | Solution | |
Power | Problematic starting | 1. Breakage of power circuit 2. Burnt transformer ;(special voltage type) 3. Melt fuse or damaged breaker 4. Damaged power switch | 1. Check the breakage section and connect the power wiring 2. Replace a transformer of the same type 3. Disconnect the power, reconnect the fuse; replace the breaker 4. Replace power switch |
Material feed-in | Unstable material feed-in | 1. Presence of sundries, garlic stalks and films or too many cloves connected together in the collection bucket. 2. Loose or breakage of fencing board at feed-in 3. Jammed axis of the feed-in cylinder, caused by remaining garlic oil 4. Defective feed-in cylinder 5. Cracked air circuit pipeline 6. Damaged time relays for feed-in or peeling time | 1. Adjust the content of sundries in the fed in material, remove the garlic stalks and films before feeding into the bucket. 2. Check the feed-in fencing board. Once a damage to the rubber board is spotted, replace it or use a standby rubber board 3. Timely clean the components in the cylinder of the feed-in bucket 4. Timely repair or replace the damaged cylinder 5. Replace the cylinder 6. Timely replace the time relay |
Problematic starting for material feed-in | 1. No entry of compressed air 2. Pressure of triad fails to reach 0.5MPa 3. Breakage of air circuit 4. Defective solenoid valve for feed-in 5. Too small flow given by the flow valve (which is located at the most right side on the pneumatic control panel at the back) 6. Defective feed-in cylinder 7. Damaged ;time relays for feed-in or peeling time 8. Numeral for the feed-in time control isn’t sufficiently large. | 1. Open the general valve for the air source 2. Turn the pressure adjusting knob of the triad clockwise until the pressure reaches 0.5MPa. 3. Replace the damaged air pipeline 4. Repair or replace the solenoid valve 5. This is a frequent occurrence, which can be solved by the following steps. Firstly, find the flow adjusting valve with two hand wheels, one large and one small. The valve is located at the most right side at the bottom of the pneumatic control panel at the back. Secondly, loose the larger hand wheel and turn the smaller one. When the smaller wheel is turn clockwise, the strength in the feed-in cylinder decreases and when it is turned counterclockwise, the value increases. When the adjustment is done appropriately, simply turn the larger wheel. 6. Repair or replace the feed-in cylinder 7. Replace the time relay, type being JS14S 99.9s220v/50Hz 8. Adjust the feed-in value, use ;“+”to increase the value and use ;“-” to decrease the value. Usually, only adjustment to the rightmost number of the time relay is necessary. Each press of the ;“+”or ;“-” can increase or decrease the value by 0.1 second. | |
Peeling | Excessively low peeling rate | 1. Garlic cloves are not dry enough or too many cloves connected together. 2. Type of garlic clove difficult to be peeled is adopted 3. Mixture of various types of garlic 4. Too small value set on the ;“peeling time control” 5. Blocked air circuit 6. Defective solenoid valve 7. Inadequate pressure for the air compressor 8. Leakage of air-spraying circuit 9. leakage of the swift joint 10. Poor tightness of the blocking plate of the material discharging, cause leakage upon peeling ;(This is a frequent fault, so please pay attention to it!) | 1.Further separate the garlic. Expose the garlic to be peeled to sunshine or bake it. 4.Increase the value for ;“peeling time control”. Usually the middle number of the time relay should be adjusted. Each press of the ;“+”or ;“-” can increase or decrease the value by 1 second. 5.Replace the air pipeline 6.Replace the solenoid valve 7.Adjust the max. pressure of the air compressor until it reaches the setting as show in III. 8.Replace the air pipeline 9.Replace the swift joint 10.This is a frequent occurrence which can be solved by the following steps. Clean the blocking board to restore to the original state. As an alternative, remove the connecting air pipeline for the discharging cylinder before dismantling the cylinder; then adjust the connecting screw rod to an appropriate length. Finally, plug on the air pipeline. Do not change the positions of air pipelines up and down. Secure the cylinder. |
Damages to cloves | 1. Too small value set for the peeling time control 2. Too small value set for the feed-in time control 3. Type of garlic clove difficult to be peeled is adopted 4. Mixture of various types of garlic 5. Garlic cloves are not dry enough, in other words, they are too wet | 1. Decrease the value for the ;“peel time control” 2. Increase the value for the ;“feed-in time control” 3. Bake or expose the garlic cloves to be peeled to sunshine. | |
Material discharging | Inflexible movement of the discharging valve | 1. Too small flow given by the flow valve 2. Leakage caused by broken pipeline 3. Defective discharging cylinder 4. Defective discharging solenoid valve 5. Loose connection between the cylinder and discharging plate 6. Defective time relays for feed-in or peeling time | 1. The solution is the same as Item 5 for ;“Problematic starting for material feed-in”. The difference lies in the adjustment to the knob for the ;“flow adjusting valve” that connects the discharging solenoid valve. 2. Replace the air pipeline 3. Replace the discharging cylinder 4. Replace the discharging solenoid valve 5. Readjust the length of the connecting screw of the cylinder and discharging board so that it reaches the sealing state 6. Replace the time relay |
Over strong blocking board for discharging | Too large flow given by the flow valve ;(which can be adjusted with the part located at the most right side at the back) | The solution is the same as Item 1 for ;“Problematic discharging”. Simply turn the discharging flow adjusting valve one or half turns. |
Please enter your demand such as Raw material type,Capacity, Feeding material size, Final product size. We will reply you as soon as possible.
- Drum Mixer Horizontal Stainless Steel Drum Mixer Flour Additive Powder Mixing machine
- Stainless Steel Multi functional Drum Type Commercial Octagonal Mixer Fully Automatic Food Seasoning Machine nut flavor mixing machine
- Continuous Drum Rotary Tumbler Mix Food Cashew Seasoning Mixer Snack Seasoning Machine